What Clients Mostly Ask
FAQs
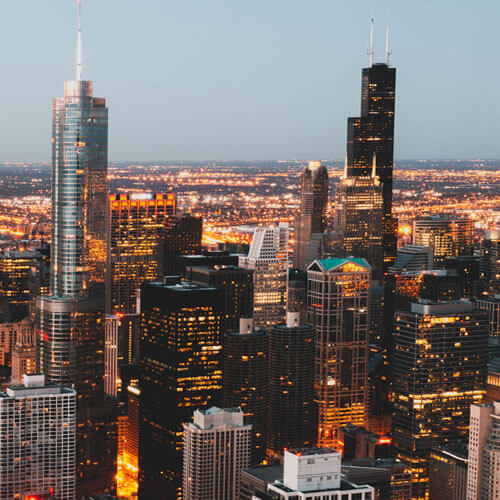
Calcined bauxite is a processed form of bauxite ore that undergoes high-temperature heating to remove moisture and impurities, resulting in a durable material suitable for various industrial applications.
The primary applications of calcined bauxite include refractory manufacturing, abrasives production, road surfacing, and welding fluxes.
Calcined bauxite differs from raw bauxite in that it has undergone a calcination process, which alters its physical and chemical properties, making it more suitable for specific industrial uses.
The advantages of using calcined bauxite include its high alumina content, hardness, and resistance to abrasion, which make it ideal for applications such as refractories and abrasives. It also offers superior performance in road surfacing due to its high skid resistance and durability.
The production and use of calcined bauxite can be sustainable if responsible mining practices are employed, and efforts are made to minimize environmental impacts throughout the production process.
Yes, calcined bauxite can be customized to meet specific application requirements, such as particle size distribution and chemical composition.
Customers can inquire about purchasing calcined bauxite products or request technical support through the company’s website, contact information, or customer service
A bauxite rotary kiln is a crucial component in the production of alumina from bauxite ore. It operates by heating bauxite ore to high temperatures in a rotating cylindrical kiln, typically fueled by coal, gas, or oil. The intense heat causes the bauxite to undergo various chemical and physical transformations, ultimately yielding alumina, which is a precursor to aluminum production. The kiln’s rotation ensures even heating and efficient processing of the bauxite ore.